Quality Management 101: Delivering Excellence
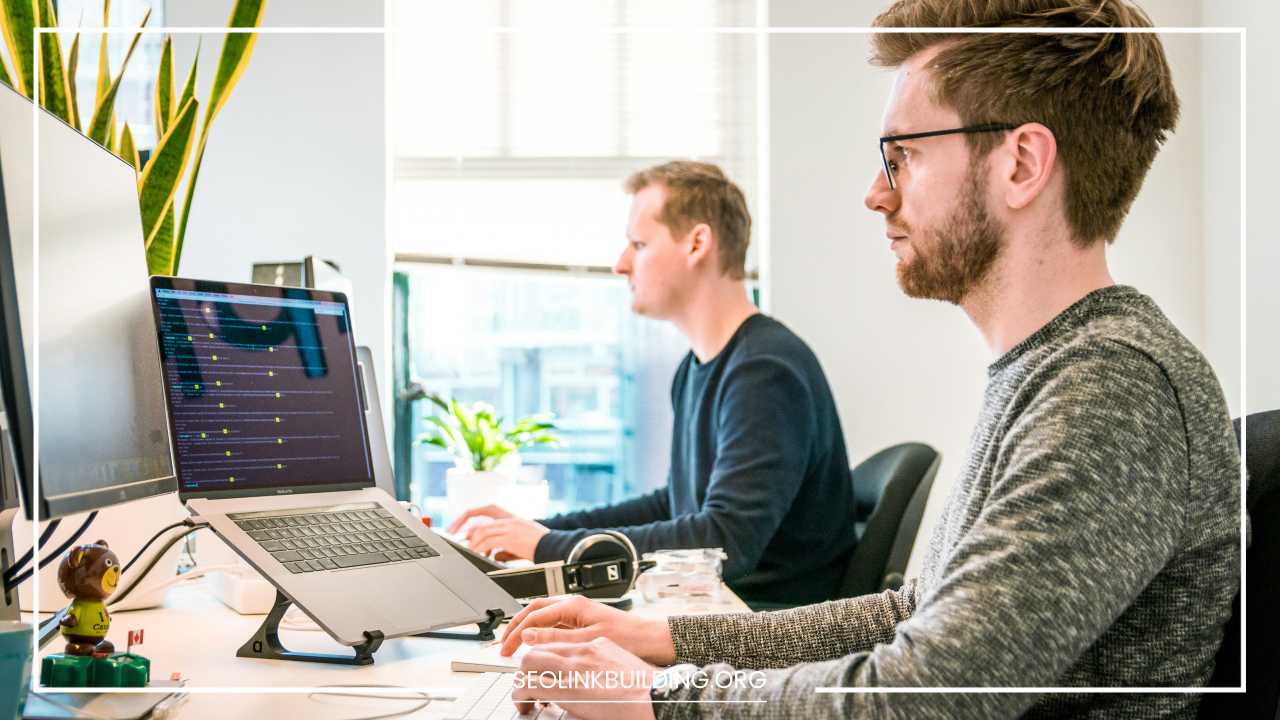
Quality Management
Quality Management 101: Delivering Excellence, One Process at a Time
In today’s hyper-competitive landscape, delivering quality products and services is the cornerstone of any successful organization. Customers wield more buying power than ever before, with ever-evolving expectations. This is where Quality Management (QM) steps into the spotlight.
QM isn’t just about checking boxes on a production line; it’s a holistic approach that ensures everything you do, from the initial spark of an idea to post-sales support, meets the highest standards. It’s about fostering a culture of continuous improvement that permeates every facet of your organization, from the CEO’s office to the factory floor.
Demystifying Quality Management
At its core, QM is the act of overseeing processes to guarantee consistent quality outputs. It encompasses a range of activities, including:
- Quality Planning: Defining what “quality” means for your specific products or services and establishing measurable objectives. This involves understanding customer needs, translating them into concrete goals, and outlining the resources required to achieve them.
- Quality Control: This is the active phase of monitoring and evaluating processes to identify and rectify any issues that might compromise quality. It involves activities like inspections, testing, and data analysis.
- Quality Assurance: Think of this as the preventative arm of QM. It’s about implementing proactive measures to prevent defects and ensure consistent quality from the get-go. This involves activities like risk assessments, process audits, and establishing clear quality standards.
- Quality Improvement: This is the continuous pursuit of excellence. It involves analyzing processes to identify areas for improvement, implementing changes, and measuring the effectiveness of those changes. It’s a never-ending cycle that pushes the boundaries of what’s possible.
These four pillars work together to form a foundation for a robust Quality Management System (QMS). A QMS is a documented framework that outlines your organization’s commitment to quality and the specific procedures you follow to achieve it. It serves as a roadmap for ensuring consistent quality across all your operations.
The Compelling Case for Quality Management
The benefits of implementing a strong QM system are far-reaching and demonstrably positive:
- Customer Satisfaction is King: Happy customers translate to repeat business and positive word-of-mouth marketing, which is the holy grail in today’s competitive landscape. QM ensures your offerings consistently meet or exceed customer expectations, fostering loyalty and trust.
- Cost Reduction Through Prevention: Imagine the financial burden of fixing defects after the fact. QM helps you prevent defects from occurring in the first place, saving you significant resources in the long run. This translates to reduced rework costs, lower warranty claims, and improved material utilization.
- Enhanced Efficiency is Key: Streamlined processes through QM lead to improved operational efficiency and productivity. By identifying and eliminating bottlenecks, you can get products and services out the door faster, meeting customer demands more effectively.
- Data-Driven Decisions for Better Outcomes: QM empowers you to make informed decisions based on real data collected through process monitoring and quality control activities. This data becomes the fuel for continuous improvement, allowing you to identify areas for optimization and make adjustments strategically.
- The Competitive Edge You Crave: In a crowded marketplace, a reputation for quality sets you apart from the competition. Customers are willing to pay a premium for products and services they can rely on, and a strong QM system paves the way for achieving that level of trust and reliability.
Building a Quality Management System: A Step-by-Step Guide
The good news is that implementing QM doesn’t have to be an overwhelming proposition. Here’s a roadmap to guide you through the process:
-
Define Your Quality Policy: This is a clear, concise statement that outlines your organization’s unwavering commitment to quality. It should be communicated to all employees, displayed prominently, and reviewed periodically to ensure continued relevance.
-
Identify Your Customer Needs: Understanding your customer’s expectations is paramount. Conduct market research, gather feedback through surveys, and actively listen to customer concerns via social media platforms and support channels. Analyze this data to identify key customer needs and translate them into actionable insights for your quality objectives.
-
Develop Measurable Quality Objectives: SMART objectives are the heart of any successful QM system. Specific, Measurable, Achievable, Relevant, and Time-bound objectives ensure you’re working towards tangible goals that align with your overall quality policy and customer needs.
-
Embrace a Quality Management System Framework: Choose a QMS framework that aligns with your organization’s size, industry, and specific needs. Popular options include ISO 9001, which provides a comprehensive framework for quality management systems, and Six Sigma, a data-driven methodology focused on eliminating defects and achieving near-perfect quality.
-
Standardize Your Processes: Document your key processes in detail, including roles, responsibilities, and step-by-step instructions with clear flowcharts or process maps. This ensures consistency, reduces errors, and empowers employees to perform their tasks effectively.
-
Invest in Employee Training and Development: Your employees are the backbone of your QM system. Invest in training them on the principles of QM, your specific QMS procedures, and the quality tools you’ll be utilizing. Empower them to identify and suggest improvements, fostering a sense of ownership and accountability.
-
Monitor and Measure Continuously: Quality is a journey, not a destination. Regularly monitor your processes using data collection methods like control charts. Analyze the data to identify trends, potential issues, and areas for improvement. This data becomes the cornerstone for your continuous improvement initiatives.
-
Embrace a Culture of Continuous Improvement: Foster a culture where continuous improvement is embedded in your organization’s DNA. Encourage employees to identify areas for improvement, propose solutions, and participate in pilot programs to test those solutions. Celebrate successes and recognize employees who actively contribute to the ongoing improvement process.
The Quality Management Toolkit: Powerful Tools for Success
There’s a vast array of tools and techniques available to support your QM efforts. Here are a few key examples:
- Statistical Process Control (SPC): This data-driven approach allows you to monitor and control processes by identifying variations that could lead to defects. Control charts are a popular SPC tool that visually represent process data, helping you identify trends and potential issues before they escalate.
- Failure Mode and Effects Analysis (FMEA): This proactive method helps you anticipate potential failures in a process and implement preventative measures to mitigate risks. By identifying potential failure points, their severity, and occurrence likelihood, you can develop strategies to safeguard against them.
- Six Sigma: This data-driven methodology focuses on eliminating defects and achieving near-perfect quality through a structured, five-phase approach (Define, Measure, Analyze, Improve, Control or DMAIC). It utilizes various statistical tools to identify and eliminate variations in processes, leading to significant quality improvements.
- Cause-and-Effect Diagram (Ishikawa Fishbone): This visual tool helps you identify the root causes of quality problems. It resembles a fish skeleton, with the problem at the head and branches leading to potential causes categorized by factors like people, machines, methods, materials, and measurement.
- 5 Whys Technique: This iterative questioning method helps you delve deeper into the root cause of a problem. By repeatedly asking “why” something happened, you can peel back the layers and identify the underlying cause that needs to be addressed.
Building a Sustainable Quality Culture
Implementing a robust QM system is just the first step. The true challenge lies in building a sustainable culture of quality where continuous improvement becomes ingrained in your organization’s DNA. Here are some key strategies to consider:
- Leadership Commitment: Leaders set the tone for the organization. When senior management demonstrates a strong commitment to quality, it sends a powerful message to employees and reinforces the importance of QM initiatives.
- Communication and Transparency: Open communication is vital. Regularly communicate QM goals, progress updates, and success stories to all employees. This fosters a sense of ownership and keeps everyone engaged in the quality journey.
- Recognition and Rewards: Acknowledge and reward employees who actively participate in QM initiatives and contribute to improvements. This reinforces the desired behaviors and motivates others to follow suit.
- Empowerment and Ownership: Empower employees to take ownership of their work and identify opportunities for improvement. Provide them with the resources and training they need to contribute meaningfully.
The Ever-Evolving Landscape of Quality Management
The world of QM is constantly evolving. Emerging technologies like Artificial Intelligence (AI), Big Data, and the Internet of Things (IoT) are transforming how organizations approach quality. Here are some exciting trends to watch:
- Predictive Quality: Leveraging AI and Big Data, organizations can analyze historical data to predict potential quality issues before they occur. This proactive approach allows for preventative measures and minimizes the risk of defects.
- Real-Time Quality Monitoring: IoT sensors embedded in machines and products can provide real-time data on performance and potential issues. This allows for immediate corrective actions and ensures consistent quality throughout the production process.
- Customer-Centric Quality: In today’s digital age, customer feedback is readily available. Organizations can leverage social media sentiment analysis and online reviews to glean valuable insights into customer perceptions of quality. By incorporating this data into their QM efforts, they can ensure their offerings are continuously aligned with evolving customer expectations.
Final Word: The Journey to Excellence
Building a strong QM culture takes time, dedication, and a continuous commitment to improvement. By prioritizing quality and implementing the strategies outlined above, you can empower your organization to:
- Deliver exceptional products and services that consistently meet or exceed customer expectations.
- Foster a culture of innovation and continuous improvement, driving long-term success.
- Reduce costs associated with rework, scrap, and warranty claims.
- Enhance employee engagement and satisfaction through a focus on quality.
- Achieve a sustainable competitive advantage in an ever-evolving marketplace.
Remember, quality is not a destination; it’s a journey. By embracing a culture of continuous improvement and leveraging the power of quality management tools and techniques, you can ensure your organization is well-positioned to deliver excellence, one process at a time.
Additional Resources:
In addition to the resources mentioned previously, here are some additional materials to help you on your Quality Management journey:
- The American Society for Quality (ASQ) offers a wealth of resources on quality management, including training courses, certification programs, and publications: https://asq.org/
- The International Organization for Standardization (ISO) provides information on various quality management standards, including ISO 9001: https://www.iso.org/
- The Chartered Quality Institute (CQI) is a professional body for quality professionals, offering resources and guidance on implementing quality management systems: https://www.quality.org/
By taking advantage of these resources and the vast array of knowledge available on Quality Management, you can embark on a path to continuous improvement and achieve operational excellence within your organization.